Advanced manufacturing is increasingly a data rich endeavor, with big data analytics addressing critical challenges in high-tolerance assembly, operation planning, quality control and supply chains. Modern aircraft assembly is at the forefront of integrating big data into manufacturing, with advances in metrology accelerating aircraft manufacturing processes in recent years, for example in large composite structures, in fuselage skin panels, and in the wing box. Machine learning is a particularly promising tool for extracting actionable patterns in vast quantities of high-dimensional data that are difficult to visualize and/or interpret. In the BARC, we are collaborating with experts at Boeing to capitalize on their wealth of data for a number of high priority applications in aircraft manufacturing. These projects include predicting shims to accelerate aircraft production rates, bracket standardization to streamline design and reduce costs, automated carbon fiber placement for advanced composite manufacturing, and designing advanced scheduling algorithms for collaborative robots. These collaborations are already leading to new and innovative approaches that are being deployed in several aircraft production lines.
Project: Predictive Shimming with Machine Learning and Sparse Sensing
In aircraft manufacturing, gaps between parts commonly occur as a natural consequence of modular manufacturing, assembly, and transport. These gaps are painstakingly measured using costly laser scans for the precise manufacture of shims (filler components) to fill these gaps. This process is known as predictive shimming, and it adds a significant amount of time to aircraft production. As an alternative, machine learning can be used to mine patterns from historical data and reduce the burden of data collection and processing in future aircraft. Our approach uses robust principal component analysis to first learn spatial gap correlations from historical data, and then optimizes sensor locations in a way that maximizes the amount of gap information within these reduced measurements. Our method has demonstrated remarkable success on Boeing production data, predicting 99% of gaps in new aircraft wing to body join instances using only 3% of the original measurements. This has the potential to dramatically reduce the time to manufacture aircraft, resulting in significant savings. Our predictive shimming algorithms are currently being applied to several aircraft production lines.
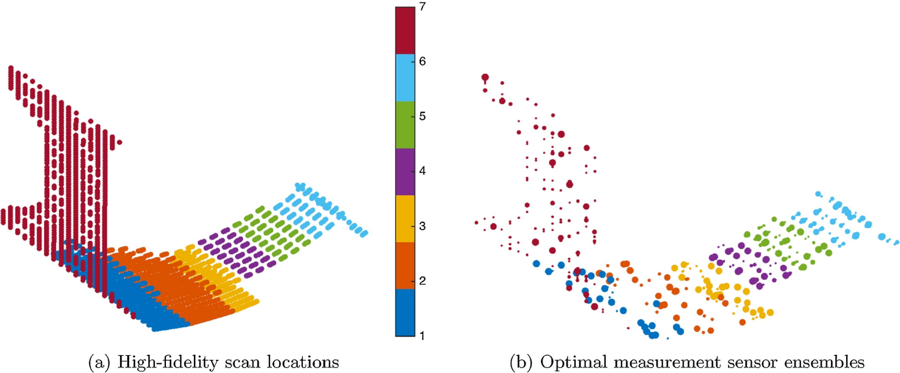
This image depicts the dramatic reduction in sensor ensembles (b) learned from the original scan locations (a). Reproduced with permission from Manohar et al, Journal of Manufacturing Systems 2018.
Project: Bracket Standardization
In aircraft manufacturing, it is common to design a new bracket whenever one encounters a new joint or intersection. However, this leads to a large number of unique brackets, which are time consuming and expensive to design and produce. In this work, we analyze bracket sets from historical aircraft data and design algorithms to hierarchically group them by similarity, with the goal of creating a relatively small set of representative brackets that can be used for most applications. This will reduce design time and result in cheaper parts that are produced and used in bulk.
Project: Deep learning for automated in-process inspection of composite layup
Composite materials, comprising carbon-fiber reinforced polymers, are becoming increasingly popular in manufacturing aircraft structures due to their combination of high strength and low density. The manufacturing process is, however, challenging in terms of quality control, which makes accurate in-process inspection of composite parts particularly important.
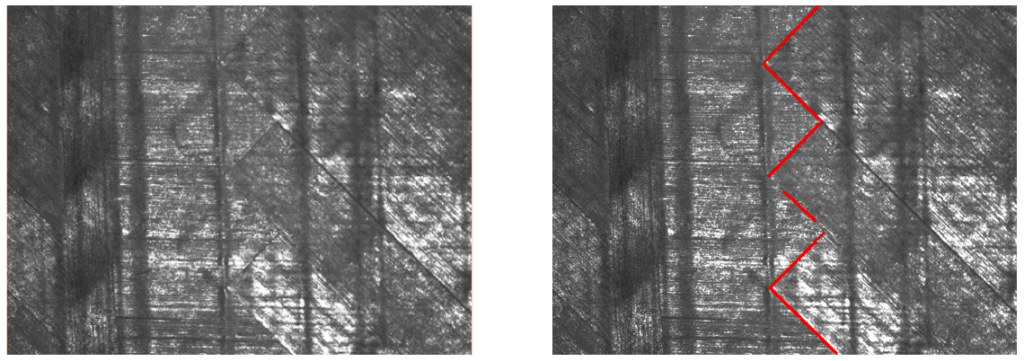
The researchers are developing deep learning-based methods for visual inspections of tow boundaries that form the edges of the individual plies. The current metrology-based automated tow boundary inspection system needs manual review for about 10% of the data. This is a time-consuming, non-value added process that holds up production. The objective is to improve the accuracy of identifying the tow ends to eliminate as much of the time-consuming manual inspections as possible. The initial results are very promising as an encoder-decoder style deep learning network provides better accuracy than the current system even without leveraging knowledge about the expected tow ends locations and orientations. The long-term goal is to develop such learning methods to automate other process inspection steps, possibly in conjunction with physics-based process modeling.
Related Publications
K. Manohar, T. Hogan, J. Buttrick, A. G. Banerjee, J. N. Kutz, S. L. Brunton, Journal of Manufacturing Systems, pages 87-95, Predicting shim gaps in aircraft assembly with machine learning and sparse sensing, Vol. 48, 2018
Krithika Manohar, Bingni W. Brunton, J. Nathan Kutz and Steven L. Brunton, IEEE Control Systems Magazine, pages 63-86, Data-Driven Sparse Sensor Placement, Vol. 38, 2018
W. Guo, K. Manohar, S. L. Brunton, A. G. Banerjee, IEEE Transactions on Knowledge and Data Engineering, pages 1403-1408, Sparse-TDA: Sparse realization of topological data analysis for multi-way classification, Vol. 30(7), 2018
Emily Clark, and Travis Askham and Steven Brunton and J. Nathan Kutz, IEEE Sensors Journal, pages 2642-2656, Greedy Sensor Placement with Cost Constraints, Vol. 19(7), 2019
Current Investigators: Sasha Aravkin, Ashis Banerjee, Steve Brunton, Nathan Kutz, Kristi Morgansen, Per Reinhall
Current Students: Jonathan Jonker, Kathleen Champion, Emily Clarke, Daniel Dylewski, Jared Callaham, Abhay Gupta, W. Guo, Ena Hodzic, Jonathan Jonker, Ekta Samani, Brian de Silva